Trisen Quality Assurance
TRISEN practices a Quality Assurance approach in our manufacturing process. QA is the methodology of prevention that evaluates various aspects of a new product introduction or service to determine the minimum standards of quality being restored by the manufacturing process at every stage of the product life cycle. We ensure products are defect-free by preventing mistakes with Quality Assurance. We are focused on providing confidence that quality requirements will be fulfilled and regulatory compliance by documenting the practices, creating a policy, training the employees, and conducting periodic audits to ensure that quality standards are met.
Quality Assurance Flow Chart
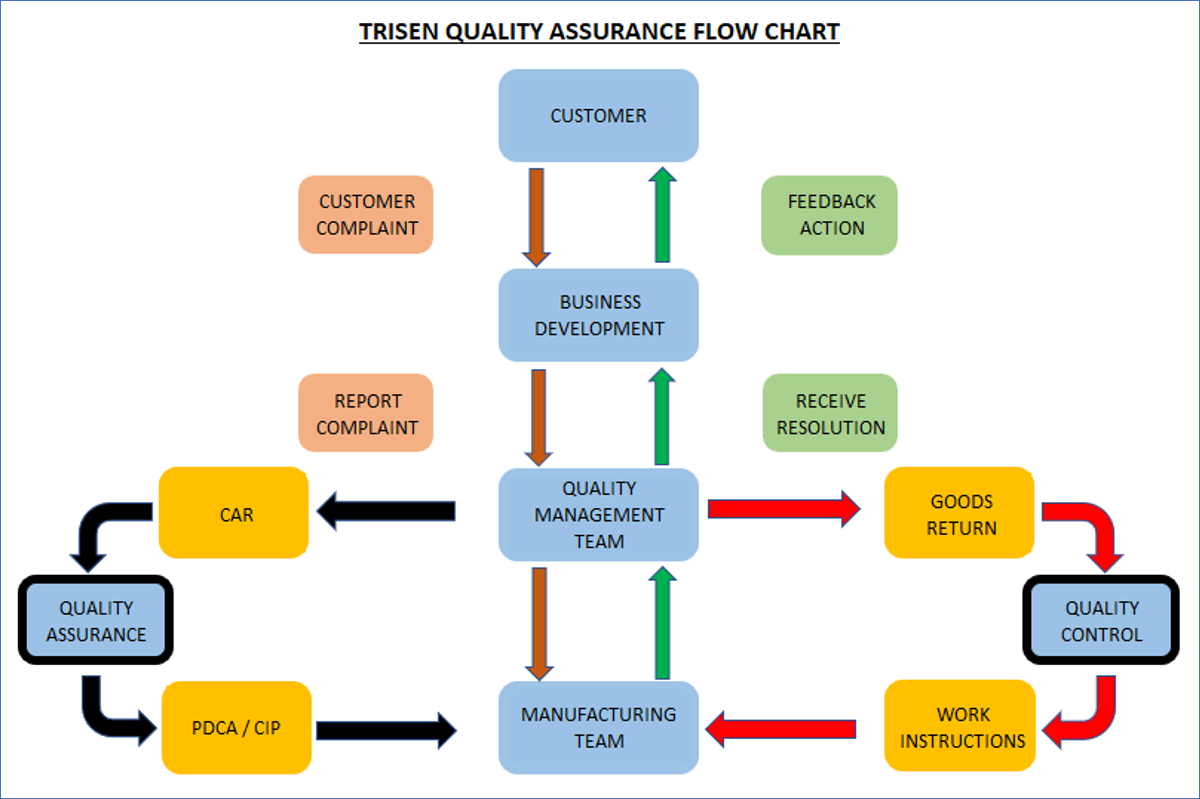
Our Quality Assurance Principles
Our Quality Assurance Process
Plan
Do
Study
Act
Plan
Do
Study
Act
Step 1
Step 2
Step 3
Step 4
Step 5
Step 6
Our Quality Assurance Tools
The Benefit of Quality Assurance
Quality Assurance (QA) Surveillance
TRISEN monitor quality assurance surveillence as an on going verification that the vendor’s quality system meets the contractual quality requirements.
Our Quality Management Plan (QMP)
The Quality Management is the act of overseeing all activities and tasks that must be accomplished to maintain a desired level of excellence. This includes the determination of a quality policy, creating and implementing quality planning and assurance, and quality control and quality improvement.
QA cannot absolutely guarantee the production of quality products.
Quality Policy
Improvement In Challenging Total Customer Satisfaction.